
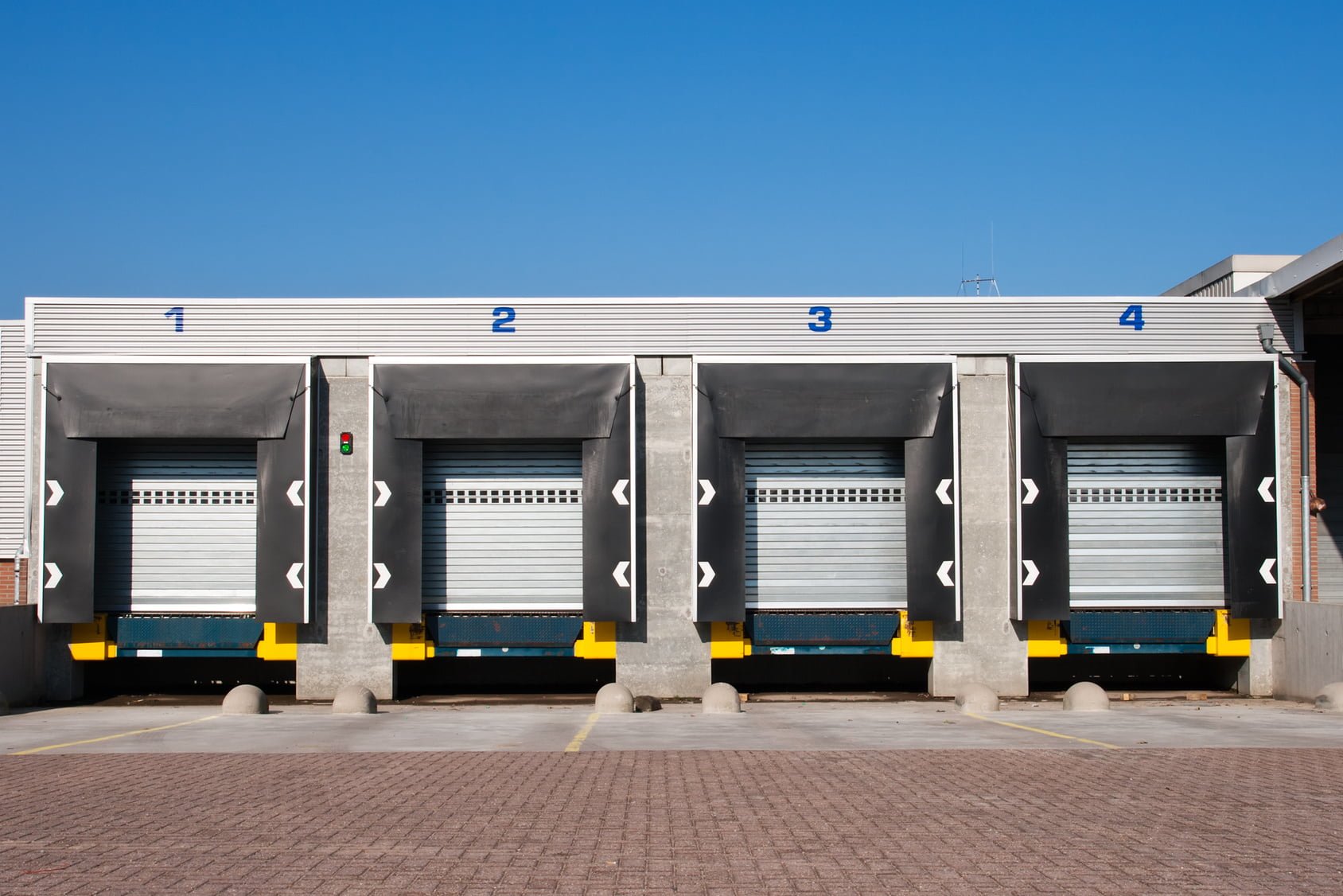

Loading docks also feature many regulations related to hazard visibility for example, employers must put visual edge markers or install guardrails at the edge of loading docks depending on their height from the ground.Ī common loading-dock-specific hazard is “trailer creep,” which occurs when the forces generated from loading or unloading activity causes a trailer to separate from the dock. Seven percent of all loading-dock accidents are caused by forklifts falling from the dock-an accident which can easily result in injury or death. Forklifts are the most common cause of OSHA safety citations in loading docks, as well as a major cause of accidents. One of the most heavily regulated activities in loading dock areas is the use of forklifts and other powered industrial trucks. They are the site of one-quarter of all workplace accidents, and the wide range of activity that occurs around them means that they are subject to a variety of intersecting hazard regulations and standards. Loading docks are often an environment in which workers must perform a variety of irregular tasks, making them a significant site for workplace hazards. Because loading bays are used in a variety of different contexts, the specific hazards that apply to them can vary significantly depending on the industry that they are servicing. These include general hazards associated with the movement of hazardous materials, ergonomic injuries, and forklift accidents, as well as site-specific accidents related to the loading bay structure itself. Most can restrain a vehicle with a pullout force of up to 30,000 lbs.The transport of materials to and from the loading dock can expose workers to a wide variety of potential hazards. When the transport vehicle backs up to the building, the dock lock attaches to the rear guard. The dock lock or vehicle restraint is mounted to the building and looks like a large hook. They prevent forklifts and other equipment from falling off the dock. Professionals also appreciate the open frame design which makes for easy cleaning and maintenance.ĭock locks and vehicle restraints are important to worker safety and enhanced productivity. It’s operated when a release chain is pulled, lifting the leveler into position. The most versatile is the mechanical leveler. These are ideal for atmospheres that experience extreme temperatures. The air bag is activated by a power button that causes the bag to inflate or deflate. Air-Powered Dock LevelersĪs the name suggests, this type of leveler uses air bag lifting technology. Hydraulic systems are also regenerative and require less maintenance than other types. They also feature a velocity fuse which keeps the leveler from descending too quickly if the truck happens to pull away unexpectedly. The unique difference of hydraulic loading dock levelers is that they are specifically designed to handle high-capacity workloads. The Most Popular Types of Loading Dock Levelers Hydraulic They’re usually made of rubber and sit on the edge of each side of the loading dock. They prevent the transport vehicle from running into the building and causing damage and injuries. The BumpersĪlthough not technically part of the loading dock leveler itself, the bumpers add a crucial level of protection. The deck is also the part that attaches to the lip to allow for the safe and efficient passage of warehouse vehicles and equipment.
Loading dock professional#
Sometimes called the ramp, it’s the section that is driven over - whether a professional is using a forklift, pallet jack, or hand truck. Probably the most important part of the loading dock leveler is the deck. Depending on the type, it’s either powered by springs or an air bladder. Otherwise known as the activation system, the push bar is the mechanical arm that pushes the deck of the leveler into place. They usually consist of a tread pattern for greater safety during transport. It’s permanently affixed to the deck of the building. The lip of the loading dock leveler extends outward and onto the floor of the transport vehicle. They are mechanical devices that are adjustable and customization. The main components of loading dock levelers are the deck, lip, push bar, and bumpers. Understanding the Parts of Loading Dock Levelers Loading areas that lack a leveler can be hazardous due to higher risks of injury and extended production time, making levelers an essential piece of equipment for most warehouses and commercial operations.

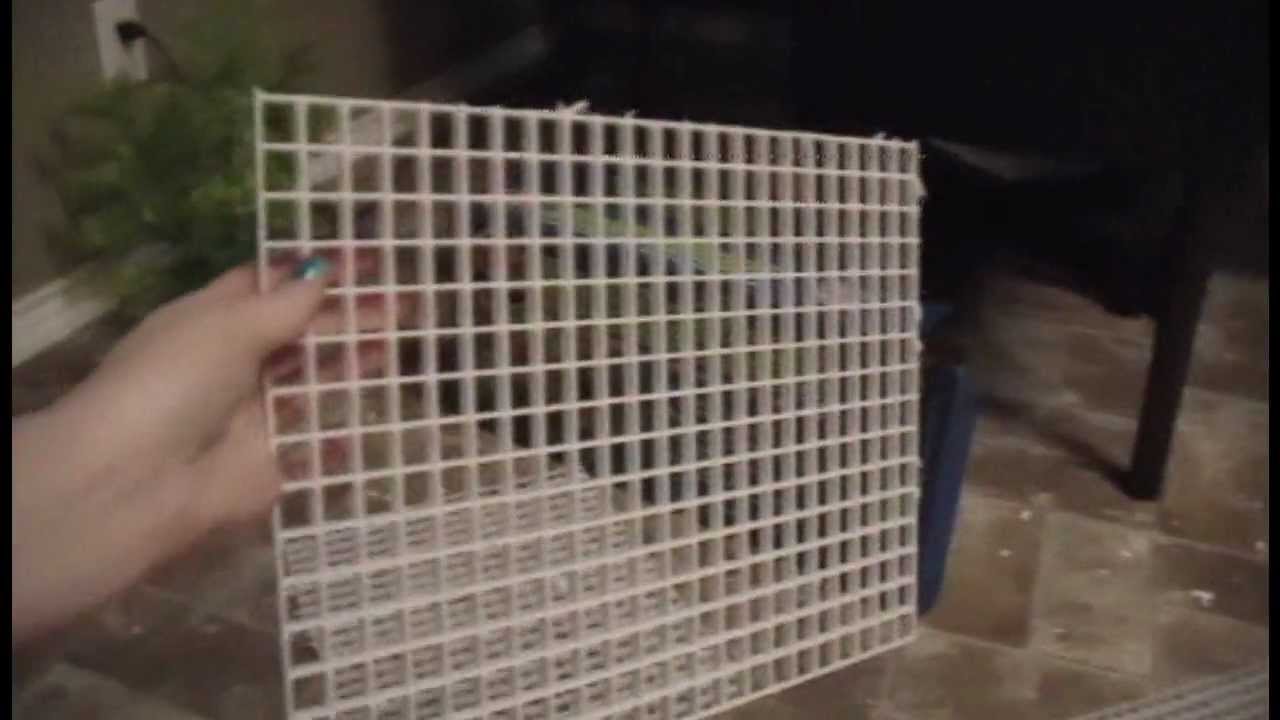
It’s an essential piece of equipment that makes it efficient to move goods and other equipment from the trailer bed onto the warehouse floor or vice versa. If you’ve ever seen a transport vehicle back up to a building, then you’ve probably seen a loading dock leveler.
